Uncategorized
September 30th, 2024 | by admin_me_wp | posted in
Uncategorized
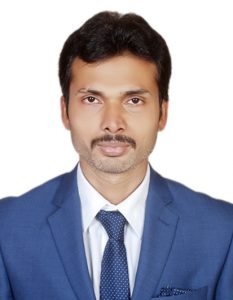
Faculty Name: Dr. Krishna Mohan Kumar
Designation: Assistant Professor
Research: Mechanical System Design
Email: kmkumar@iiti.ac.in Office: +91 731-6603359
Research Areas:
- Acoustics of Ducts and Mufflers;
- Industrial Noise and Vibration Control;
- Automotive Noise Control; and Designing for Quietness;
Biosketch:
Dr. K.M. Kumar is an Assistant Professor in the department of Mechanical Engineering atIndian Institute of Technology Indore. He received his B. Tech degree in Mechanical Engineering from Jalpaiguri Government Engineering College, in 2010 and M. Tech degree in Mechanical Engineering with Machine Design specialization from Indian Institute of Technology Guwahati, in 2012. He was awarded Ph.D. degree from Indian Institute of Science in 2019 for his thesis entitled “Direct Estimation of Acoustic Source Characteristics of the Internal Combustion Engine Exhaust System and Analysis of Complex Muffler Configurations.”
During his Ph.D., he has worked as project assistant on 5 industrial consultancy projects related to design and analysis of automotive and DG set silencers/mufflers. After his Ph.D. thesis submission, he worked on 3industrial consultancy projects as co-consultant with Prof. M. L. Munjal of Indian Institute of Science, Bengaluru. In 2018-19, Dr. Kumar delivered lectures as a co-instructor with Prof. Munjal on Acoustics of Ducts and Mufflers and Industrial Noise Control to train the practicing engineers of Faurecia Clean Mobility Centre, Bengaluru. He has published several papers in peer-reviewed international journals as well as conferences. His research interests are Acoustics of Ducts and Mufflers; Automotive Noise and Vibration Control; Industrial Noise and Vibration Control; and Designing for Quietness
RESEARCH PUBLICATIONS:
- Peer-reviewed International Journals
- M. L. Munjal and K. M. Kumar, “State of the art of rational design of efficient mufflers”, Noise Control Engineering Journal, 71(3), 169-179, 2023.
- K. M. Kumar, C. D. Gaonkar and M. L. Munjal, “Double-tuning and Experimental Validation of Rotated-Offset Inlet-Outlet Circular Chamber Muffler”, Applied Acoustics, 197, 1-16, Aug 2022, Paper Number: 108948.
- C. D. Gaonkar, D. R. Rao, K. M. Kumar and M. L. Munjal, “End Corrections for Double-Tuning of the Same-End Inlet-Outlet Muffler,” Applied Acoustics, 159, 1-10, Feb 2020, Paper Number: 107116.
- K. M. Kumar and M. L. Munjal, “Direct estimation and experimental validation of the acoustic source characteristics of turbocharged diesel engine exhaust system,” Applied Acoustics, 149, 171-180, 2019.
- K. M. Kumar and M. L. Munjal, “Direct estimation and experimental validation of the acoustic source characteristics of two-cylinder naturally aspirated diesel engine exhaust system,” Applied Acoustics, 135, 70–84, 2018.
- K. M. Kumar and M. L. Munjal, “On development of rational design guidelines for large side-inlet side-outlet perforated element mufflers,” Noise Control Engineering Journal, 66(4), 308–323, 2018.
- K. M. Kumar and M. L. Munjal, “On the crucial role of mean flow in the design of multiply-connected coaxial perforated element mufflers,” Noise Control Engineering Journal, 65(5), 462–481, 2017.
- International Conferences
- K. M. Kumar, “Double-Tuning of Co-Axial Inlet-Outlet Elliptical Chamber Muffler”29th International Congress On Sound and Vibration, Prague, Czech Republic,9–13 July 2023,1–8.
- K. M. Kumar and M. L. Munjal, “Improved Parametric Expressions for Acoustic Source Strength Level and Impedance of Turbocharged Diesel Engine Exhaust System”, Symposium on International Automotive Technology (SIAT) 2019, Pune, India, 16–18 January 2019,1–10.
- K. M. Kumar and M. L. Munjal, “Direct estimation and experimental validation of the acoustic source characteristics of 4-cylinder turbocharged diesel engine exhaust system,” 13th Western Pacific Conference on Acoustics (WESPAC-2018), New Delhi, India, 11–15 November 2018, 1–6.
- K. M. Kumar and M. L. Munjal, “A Simple Novel Method for Direct Evaluation of the Acoustic Source Impedance of the Exhaust System of a Single Cylinder Engine,” 24th International Congress On Sound and Vibration, London, 23–27 July2017,1–8.
- K. M. Kumar, “On the crucial role of higher order evanescent modes for double-tuning of same-end inlet-outlet and opposite-ends inlet-outlet elliptical chamber mufflers” 50thNational Symposium on Acoustics, VSSUT Sambalpur, India, 24–26 February 2023, 1–10.
- C. D. Gaonkar, K. M. Kumar and M. L. Munjal, “Evaluation of End-corrections for a Double-tunedRotated-Offset Inlet-Outlet Muffler,”47th National Symposium on Acoustics (NSA-2019), Cuttack, 17–19 October 2019,1–6.
- K. M. Kumar and M. L. Munjal, “1-D Acoustical Analysis of a Typical Double Flow-Reversal Commercial Muffler of a Motorcycle Engine and 3-D Validation Thereof,” 4thAutomotive Noise and Vibration Congress, Pune,8–9 November2017,1–11.
- K. M. Kumar and M. L. Munjal, “Direct Evaluation of the Engine Acoustic Source Characteristics and Validation Thereof,” 3rd Automotive Noise and Vibration Congress, Pune,28–29 January2016,1–17.
- Development of Numerical Model to Compute the Flow and Acoustic Field Inside and Outside of the Gun Barrel for Practice Ammunitions and Actual Rounds
Role: Principal investigator
Sponsoring Agency: Defence Research and Development Organization
Cost: ₹ 44,62,089
September 30th, 2024 | by admin_me_wp | posted in
Uncategorized
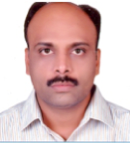
Faculty Name: Dr. Anand Parey
Designation: Professor (HAG)
Research: Mechanical System Design
Laboratory: Solid Mechanics Lab (UG), Noise and Vibrations Control Lab (PG), Gear Fault Diagnosis Lab,
Email: anand.parey@iiti.ac.in Office: +91 731-6603234
Research Areas: Condition monitoring, Signal processing of mechanical systems, Noise and vibration control
Educational Qualifications:
Ph. D. Research Topic: “Dynamic Modeling and Signal Processing of Spur Gear Vibration for the Detection of Faults”. From Industrial Tribology Machine Dynamics and Maintenance Engineering Center, Indian Institute of Technology Delhi, New Delhi, INDIA in 2005.
M.Tech. In “Maintenance Engineering” from “Maulana Azad National Institute of Technology”, Bhopal, India, in 2001, Project Topic: “Condition Monitoring of Diesel Locomotive using Vibration Analysis and Echo Pulse Measurement.”
B.E. In “Mechanical Engineering” from “Madhav Institute of Technology and Science”, Gwalior, India, in 1998.
Research Areas:
Condition monitoring, Signal processing of mechanical systems, Noise and vibration control
Work Experience:
Professor: Working as Professor in Department of Mechanical Engineering at IIT Indore, from Dec 18, 2017 till date.
Associate Professor: Worked as Associate Professor in Department of Mechanical Engineering at IIT Indore, from Sep 2012 to December 17, 2017.
Assistant Professor: Worked as Asst Prof. in Department of Mechanical Engineering at IIT Indore from Aug 3, 2009 to Sep 2012.
Assistant Manager: Worked as Asst Manager in Larsen and Toubro Ltd. Mumbai from Sep. 2008 in Heavy Engineering Division to July 2009.
Manager: Worked as Manager-Technology in Crompton Greaves Ltd. Global R&D Centre, Mumbai from April 2008 to August 2008.
Post Doctoral Fellow: Post Doctoral Fellow in University of Alberta, Edmonton, Canada from Dec 2006 to Dec 2007.
Lecturer: Worked as Lecturer in BITS-Pilani, Goa campus, Goa, India, from August 2005 to November 2006 in Mechanical Engineering Division.
Papers in peer reviewed, Scopus indexed journals
- Parey and N. Tandon, Spur gear dynamic models including defects- A review, The Shock and Vibration Digest, Vol. (35), Number (6), November-2003, PP 465-478.
- Parey, M El Badaoui, F. Guillet, and N. Tandon, Dynamic modeling of spur gear pair and application of empirical mode decomposition based stastical analysis for early detection of localized tooth defect, Journal of Sound and Vibration, 294, 2006, PP 547-561.
- Parey and N. Tandon, Impact velocity modeling and signal processing of spur gear vibration for the estimation of defect size, Mechanical Systems and Signal Processing,21(1), 2007, PP 234-243.
- Siyan Wu, Ming J Zuo, Anand Parey, “Simulation of Spur Gear Dynamics and Estimation of Fault Growth”, Journal of Sound and Vibration, 317(3), 2008, PP 608-624.
- A Parey and N Tandon,”Detection of Gear Spall Using Wavelet Transform”,
Current Development in Theory and applications of Wavelet”, Volume1,
Issue3, pp 293-308,2007.
- A. Parey and N. Tandon, “Dynamic modeling and empirical mode decomposition of spur gear vibration for early detection of crack”, International Journal of COMADEM, Volume 12, Number 4, October 2009, PP.2-9.
- Parey and N. Tandon, “Gear tooth root crack detection using Morlet wavelet”,International Journal of Electronics and Computer Engineering, Vol 1, Issue 3, pp 293-308,2010.
- Parey and R. B. Pachori,” Variable cosine windowing of intrinsic mode functions: Application to gear fault diagnosis “, Measurement, Vol. 45, Issue3, pp 415-426,2012.
- Yogesh Pandya and Anand Parey, “Failure Path Based Modified Gear Mesh Stiffness for Spur Gear pair with Tooth Root Crack”, Engineering Failure Analysis, 27 (2013), 286-296.
- Yogesh Pandya and Anand Parey, “Simulation of Crack Propagation in Spur Gear Tppth for Different Gear Parameter and its Influence on Mesh Stiffness”, Engineering Failure Analysis, 30 (2013), 124-137.
- Yogesh Pandya and Anand Parey, “ Crack behavior in a high contact ratio spur gear tooth and its effect on mesh stiffness”, Engineering Failure Analysis, 34 (2013), 69-78.
- Yogesh Pandya and Anand Parey,” Experimental investigation of spur gear tooth mesh stiffness in the presence of crack using photoelasticity technique”, Engineering Failure Analysis, 34(2013), 488-500.
- Nizar Ahamed, Yogesh Pandya and Anand Parey, “Spur gear tooth root crack detection using time synchronous averaging under fluctuating speed”, Measurement, Volume 52, June 2014, Pages 1-11.
- Anand Parey and Ram Bilas Pachori, Gear fault diagnosis based on central tendency measure of intrinsic mode functions, International Journal of COMADEM, 2014; 17(03), 15-22.
- Anand Parey, N.K. Jain and S.C. Koria, Failure analysis of air cooled condenser gearbox, Case Studies in Engineering Failure Analysis, Volume 2, Issue 2, October 2014, Pages 150-156
- Ankur Saxena, Anand Parey and Manoj Chouksey, Effect of shaft misalignment and friction force on time varying mesh stiffness of spur gear pair, Engineering Failure Analysis, 49(2015), 79-91.
- Naresh K Raghuwanshi and Anand Parey, Mesh stiffness measurement of cracked spur gear by photoelasticity technique, Measurement, 73 (2015), 439-452.
- A Parey, Vibration reduction of juicer: A case study, Noise and vibration worldwide, 46(8), 2015, 30-36.
- Saxena, A., Parey, A., Chouksey, M., “Effect of gear tooth faults on time varying mesh stiffness of spur gear pair” International journal of COMADEM , 19(1), 17-21, 2016.
- Saxena, A., Chouksey, M., Parey, A., (2016) “Study of modal characteristics of a geared rotor system” Procedia Technology 23, 225-231.
- Raghuwanshi N.K., Parey A., Experimental measurement of gear mesh stiffness of cracked spur gear by strain gauge technique, Measurement, 86 (2016) 266–275.
- Sharma, V., Parey, A., Gear crack detection using modified TSA and proposed fault indicators for fluctuating speed HYPERLINK “http://dx.doi.org/10.1016/j.measurement.2016.04.076″conditions, Measurement HYPERLINK “http://dx.doi.org/10.1016/j.measurement.2016.04.076”: Journal of the International Measurement Confederation, vol. 90, pp. 560-575, 2016
- Saxena, A., Parey, A., HYPERLINK “http://dx.doi.org/10.1016/j.engfailanal.2016.09.003″Chouksey HYPERLINK “http://dx.doi.org/10.1016/j.engfailanal.2016.09.003”, M., Time varying mesh stiffness calculation of spur gear pair considering sliding friction and spalling HYPERLINK “http://dx.doi.org/10.1016/j.engfailanal.2016.09.003″defects, Engineering HYPERLINK “http://dx.doi.org/10.1016/j.engfailanal.2016.09.003” Failure Analysis, vol. 70, pp. 200-211, 2016
- Sharma V., Parey A. HYPERLINK “http://dx.doi.org/10.1177/1475921716679802.”, , HYPERLINK “http://dx.doi.org/10.1177/1475921716679802.”Gearbox fault diagnosis by application of rms based probability density function and entropy measures under various fluctuating speeds, Structural Health Monitoring, 16(6), 1-14, 2016
- Saxena, HYPERLINK “http://dx.doi.org/10.1016/j.mechmachtheory.2016.10.006” , HYPERLINK “http://dx.doi.org/10.1016/j.mechmachtheory.2016.10.006” HYPERLINK “http://dx.doi.org/10.1016/j.mechmachtheory.2016.10.006″Chouksey HYPERLINK “http://dx.doi.org/10.1016/j.mechmachtheory.2016.10.006”, M. , Parey, A., Effect of mesh stiffness of healthy and cracked gear tooth on modal and frequency response characteristics of geared rotor system, Mechanism and Machine Theory, vol. 107, pp. 261-273, 2017
- Raghuwanshi HYPERLINK “http://www.sciencedirect.com/science/article/pii/S1877705816346458”, N.K., Parey HYPERLINK “http://www.sciencedirect.com/science/article/pii/S1877705816346458″A, Effect HYPERLINK “http://www.sciencedirect.com/science/article/pii/S1877705816346458” of Back-Side Contact on Mesh Stiffness of Spur Gear Pair by Finite Element Method, Procedia Engineering, vol. 173, pp. 1538-1543, 2017
- Sharma, R.B., Parey, A. HYPERLINK “http://dx.doi.org/10.1016/j.proeng.2016.12.250”, Condition HYPERLINK “http://dx.doi.org/10.1016/j.proeng.2016.12.250” Monitoring of Gearbox using Experimental Investigation of Acoustic Emission Technique, Procedia Engineering, vol. 173, pp. 1575-1579, 2017
- Sharma, HYPERLINK “http://dx.doi.org/10.1016/j.ymssp.2016.08.015” , HYPERLINK “http://dx.doi.org/10.1016/j.ymssp.2016.08.015” Parey, A. , Frequency domain averaging based experimental evaluation of gear fault without tachometer for fluctuating speed conditions, Mechanical Systems and Signal Processing, vol. 85, pp. 278-295, 2017
- Singh, A., Parey, A. HYPERLINK “http://dx.doi.org/10.1049/iet-smt.2016.0291”, Gearbox HYPERLINK “http://dx.doi.org/10.1049/iet-smt.2016.0291” fault diagnosis under fluctuating load conditions with independent angular re-sampling technique, continuous wavelet transform and multilayer perceptron neural network, IET Science, Measurement and Technology, vol. 11(2), pp. 220-225, 2017
- Sharma, R.B., Parey, A., Tandon, N. HYPERLINK “http://dx.doi.org/10.1016/j.jsv.2017.01.010”, Modelling HYPERLINK “http://dx.doi.org/10.1016/j.jsv.2017.01.010” of acoustic emission generated in involute spur gear pair, Journal of Sound and Vibration, vol. 393, pp. 353-373, 2017
- Raghuwanshi, N. K., Parey, A, Experimental measurement of spur gear mesh stiffness using digital image correlation technique, Measurement, vol.111, pp. 93-104, 2017.
- Sharma, V. , Parey, A. , Gearbox fault diagnosis using RMS based probability density function and entropy measures for fluctuating speed conditions, Structural Health Monitoring, vol. 16(6), pp. 682-695, 2017.
- Sharma, R.B., Parey, A., Modelling of acoustic emission generated by crack propagation in spur gear, Engineering Fracture Mechanics, vol. 182, pp. 215-228, 2017.
- Sharma, V. , Parey, A. , Case study on the effectiveness of gear fault diagnosis technique for gear tooth defects under fluctuating speed, IET Renewable Power Generation, vol 11(14), pp. 1841-1849, 2017.
- Sharma, R.B., Parey, A., Modelling of acoustic emission generated due to pitting on spur gear, Engineering Failure Analysis, volume 86, pp. 1-20, 2018.
- Saxena, A. , Chouksey, M. , Parey, A., Measurement of FRFs of coupled geared rotor system and the development of an accurate finite element model, Mechanism and Machine Theory, vol. 123, pp. 66-75, 2018.
- Raghuwanshi, N.K., Parey, A., Experimental measurement of mesh stiffness by laser displacement sensor technique, , vol. 128, pp. 63-70, 2018.
- Singh, A., Parey, A., Gearbox fault diagnosis under non-stationary conditions with independent angular re-sampling technique applied to vibration and sound emission signals, Applied Acoustics, vol. 144, pp. 11-22, 2019.
- Sharma, R.B., Parey, A., Modelling of acoustic emission generated in rolling element bearing, Applied Acoustics, vol. 144, pp. 96-112, 2019.
- Sharma, V., Parey, A., Evaluating the performance of signal processing techniques to diagnose fault in a reciprocating compressor under varying speed conditions, Advances in Intelligent Systems and Computing, vol. 748, pp. 171-183, 2019.
- Parey, A., Singh, A., Gearbox fault diagnosis using acoustic signals, continuous wavelet transform and adaptive neuro-fuzzy inference system, Applied Acoustics, vol. 147, pp. 133-140, 2019.
- Raghuwanshi, N.K., Parey, A., A New Technique of Gear Mesh Stiffness Measurement Using Experimental Modal Analysis, Journal of Vibration and Acoustics, Transactions of the ASME, vol. 141(2),021018, 2019.
- Sharma, V., Parey, A., Performance evaluation of decomposition methods to diagnose leakage in a reciprocating compressor under limited speed variation, Mechanical Systems and Signal Processing, vol. 125, pp. 275-287, 2019.
- Ramteke, D.S., Parey, A., Pachori, R.B., Automated gear fault detection of micron level wear in bevel gears using variational mode decomposition, Journal of Mechanical Science and Technology, vol 33 (12), pp. 5769-5777, 2019.
- Dewangan HYPERLINK “https://www.scopus.com/authid/detail.uri?authorId=57211494043&eid=2-s2.0-85074126412”, P., Parey, A., Hammami, A., Chaari, F., Haddar, M., Damage detection in wind turbine gearbox using modal strain energy, Engineering Failure Analysis, vol 107, 2020.
- Sharma, V., Parey, A., Extraction of weak fault transients using variational mode decomposition for fault diagnosis of gearbox under varying speed, Engineering Failure Analysis, vol. 107, 2020.
- Dewangan HYPERLINK “https://www.scopus.com/authid/detail.uri?authorId=57211494043”, P., Parey, A., Hammami, A., Chaari, F., Haddar, M., Dynamic characteristics of a wind turbine gearbox with amplitude modulation and gravity effect: Theoretical and experimental investigation, Mechanism and Machine Theory, 2022, 167, 104468
- Ramteke, D.S., Pachori, R.B., Parery, A., Automated Gearbox Fault Diagnosis Using Entropy-Based Features in Flexible Analytic Wavelet Transform (FAWT) Domain, Journal of Vibration Engineering and Technologies, 2021, 9(7), pp. 1703–1713
- Thakur, V.S., Kankar, P.K., Parey, A., Jain, A., Jain, P.K., Force and vibration analysis in biomechanical preparation of root canals using reciprocating endodontic file system: In vitro study, Proceedings of the Institution of Mechanical Engineers, Part H: Journal of Engineering in Medicine, 2022, 236(1), pp. 121–133
- Gupta, P., Parey, A., Prediction of sound transmission loss of cylindrical acoustic enclosure using statistical energy analysis and its experimental validation, Journal of the Acoustical Society of America, 2022, 151(1), pp. 544–560
- Dewangan HYPERLINK “https://www.scopus.com/authid/detail.uri?authorId=57211494043”, P., Parey, A., Hammami, A., Chaari, F., Haddar, M., Dynamic Response Computation of a Wind Turbine Gearbox Under Variable Speed Conditions and its Experimental Validation, Journal of Vibration Engineering and Technologies, 2022
- Kumar, A., Parey, A., Kankar, P.K., Supervised Machine Learning Based Approach for Early Fault Detection in Polymer Gears Using Vibration Signals, Mapan – Journal of Metrology Society of India, 2023, 38(2), pp. 383–394
- Gupta, P., Parey, A., Prediction of sound transmission loss of conical acoustic enclosure using statistical energy analysis and its experimental validation, JVC/Journal of Vibration and Control, 2023, 29(9-10), pp. 2277–2289
- Thakur, V.S., Kankar, P.K., Parey, A., Jain, A., Jain, P.K., The implication of oversampling on the effectiveness of force signals in the fault detection of endodontic HYPERLINK “https://www.scopus.com/record/display.uri?eid=2-s2.0-85164907756&origin=resultslist&sort=plf-f”instruments during RCT, Proceedings of the Institution of Mechanical Engineers, Part H: Journal of Engineering in Medicine, 2023
- Kumar, A., Parey, A., Kankar, P.K., A New Hybrid LSTM-GRU Model for Fault Diagnosis of Polymer Gears Using Vibration Signals, Journal of Vibration Engineering and Technologies, 2023
- Gupta, P., Parey, A., Prediction of sound transmission loss of hemispherical shell using statistical energy analysis and its experimental validation, Measurement: Journal of the International Measurement Confederation, 2022, 204,
- Rana, V., Petare, A., Kumar Jain, N., Parey, A., Using abrasive flow finishing process to reduce noise and vibrations of cylindrical and conical gears, Proceedings of the Institution of Mechanical Engineers, Part B: Journal of Engineering Manufacture, 2022, 236(10), pp. 1341–1354
- Gangsar HYPERLINK “https://www.scopus.com/authid/detail.uri?authorId=56414903100”, P., Chouksey, M., Parey, A., Ali, Z., Diagnostics of Combined Mechanical and Electrical Faults of an Electromechanical System for Steady and Ramp-Up Speeds, Journal of Vibration Engineering and Technologies, 2022, 10(4), pp. 1431–1450
- Kumar, A., Parey, A., Kankar, P.K., Polymer Gear Fault Classification Using EMD-DWT Analysis Based on Combination of Entropy and Hjorth Features, Indian Journal of Pure and Applied Physics, 2022, 60(4), pp. 339–346
- Thakur, V.S., Kankar, P.K., Parey, A., Jain, A., Kumar Jain, P., Numerical analysis of HYPERLINK “https://www.scopus.com/record/display.uri?eid=2-s2.0-85122701567&origin=resultslist&sort=plf-f”WaveOne HYPERLINK “https://www.scopus.com/record/display.uri?eid=2-s2.0-85122701567&origin=resultslist&sort=plf-f” Gold and 2Shape endodontic files during root canal treatment, Proceedings of the Institution of Mechanical Engineers, Part H: Journal of Engineering in Medicine, 2022, 236(3), pp. 329–340
- Thakur, V.S., Kankar, P.K., Parey, A., Jain, A., Jain, P.K., Prediction of Apical Extent Using Ensemble Machine Learning Technique in the Root Canal through Biomechanical Preparation: In-vitro Study, Indian Journal of Pure and Applied Physics, 2022, 60(12), pp. 973981
- Kumar, A., Parey, A., Kankar, P.K., Effect of teeth modifications and gear-paired materials on vibration and acoustic characteristics of polymer gears, Journal of the Brazilian Society of Mechanical Sciences and Engineering, 2023, 45(12), 642
- Ramteke, D.S., Parery, A., HYPERLINK “https://www.scopus.com/authid/detail.uri?authorId=14632337000″Pachori HYPERLINK “https://www.scopus.com/authid/detail.uri?authorId=14632337000”, R.B.,A New Automated Classification Framework for Gear Fault Diagnosis Using Fourier–Bessel Domain-Based Empirical Wavelet Transform, Machines, 2023, 11(12), 1055
- Kumar, A., Parey, A., Kankar, P.K., Early pitting fault detection for polymer gears using kurtosis-VMD based condition indicators, Proceedings of the Institution of Mechanical Engineers, Part O: Journal of Risk and Reliability, 2024
- Kumar, A., Parey, A., Kankar, P.K., A New Hybrid LSTM-GRU Model for Fault Diagnosis of Polymer Gears Using Vibration Signals, Journal of Vibration Engineering and Technologies, 2024, 12(2), pp. 2729–2741
- Raghuwanshi HYPERLINK “https://www.scopus.com/authid/detail.uri?authorId=56732731700”, N.K., Yadav, S.K., Jayaswal, P., Parey, A., Noise effects, analysis and control in hospitals – A review, Noise and Vibration Worldwide, 2024, 55(3), pp. 123–134
- Haddar, M., Jorani, R.M., Parey, A., Chaari, F., Haddar, M., Experimental evaluation for detecting bevel gear failure using univariate statistical control charts, Journal of the Brazilian Society of Mechanical Sciences and Engineering, 2024, 46(4), 233
Papers in peer reviewed, scopus indexed conferences
- Parey and N. Tandon, “ On line diagnostics of gear errors”, International conference on e- manufacturing held at Bhopal, 17-19 Nov. 2002, PP 480-484.
- Parey and N. Tandon, “ Impact velocity modeling of gear vibration to estimate defect width”, International Symposium on Stability Control of Rotating Machinery-2 held at Gdansk, Poland, 4-8 August 2003, PP 428-435.
- Parey and N. Tandon, “ Dynamic modeling of spur gear including a crack”, International Symposium on Stability Control of Rotating Machinery-3 held at Cleveland, Ohio, USA, 19-23 September 2005, PP 114-123.
- Anand Parey and Ram Bilas Pachori, “Modified Empirical Mode Decomposition for Improved Fault Diagnosis”, The 8th IFTOMM International Conference on Rotor Dynamics, Sept. 12-15, 2010, Seoul, South Korea.
- Y Pandya and A Parey, “Fault detection of a two-stage gearbox with artificially induced gear crack using vibration monitoring”, 5th Indian International Conference on Artificial Intelligence, December 14-16, 2011, Tumkur, India.
- Yogesh Pandya and Anand Parey, “Finite element analysis and numerical simulation of spur gear pair with tooth root crack to calculate mesh stiffness,” ASME 2012 International Mechanical Engineering Congress and Exposition, IMECE 2012, November 9-12, Houston, Texas, USA.
- Ankur Saxena, Anand Parey, Amod C Umarikar, ” Modeling of gear sets using bond graph approach”,2nd International Conference on Intelligent Robotics, Automation and Manufacturing, December 16-18, 2013, Indore, India.
- Naresh k Raghuwanshi, and Anand Parey, ” Radial location of strain gauge on cracked tooth root of spur gear for accurate determination of stress intensity factor”,2nd International Conference on Intelligent Robotics, Automation and Manufacturing, December 16-18, 2013, Indore, India.
- Vikas Sharma and Anand Parey,” Study of root tooth crack in thin walled spur gear on mode shapes”,2nd International Conference on Intelligent Robotics, Automation and Manufacturing, December 16-18, 2013, Indore, India.
- Saxena, M. Chouksey, A. Parey, “Modal analysis of geared rotor system using finite element method”, 5thNirma University International Conference on Engineering (NUICONE 2015), Ahmedabad, India, 26 – 28 November, 2015.
- Saxena, A. Parey, M. Chouksey, “Study of modal characteristics of a geared rotor system”, 3rd International Conference on Innovations in Automation and Mechatronics Engineering, (ICIAME 2016).
- Sharma R. B., Parey A., “Gear fault diagnosis using probability density functions and entropy measures for gear acoustic emission signal”, Vibration in Rotating Machinery- VIRM11, University Place, University of Manchester, London, 2016.
- Sharma R. B., Parey A., “A novel technique based on statistical parameters using acoustic emissions for the detection of incipient gear fault”, Proceedings of the 12th International Conference on Vibration Problems, IIT Guwahati, 2015.
- Sharma V., Parey A., “Gearbox fault diagnosis by amplitude based probability density function for cracked pinion vibrations at fluctuating speeds”, Proceedings of the 17th ISME Conference on Advanced in Mechanical Engineering, IIT Delhi, 2015.
- Sharma V., Parey A., “A review of gear fault diagnosis using various condition monitoring indicators”, Proceedings of the 12th International Conference on Vibration Problems, IIT Guwahati, 2015.
- Sharma V., Parey A., “Fault diagnosis of gearbox using various condition monitoring indicators for non-stationary speed conditions: A comparative analysis”, Proceedings of the 2nd International and 17th National Conference on Machines and Mechanisms (iNaCoMM 2015), IIT Kanpur, 2015.
- Sharma V., Parey A., “Frequency domain averaging based experimental evaluation of gear fault without tachometer for fluctuating speeds”, Vibration in Rotating Machinery- VIRM11, University Place, University of Manchester, London, 2016.
- Gupta, P., Parey, A., Experimental Investigation of Sound-Absorbing Material of Different Surface Shapes on Noise Reduction Performance of an Acoustic Enclosure, Lecture Notes in Mechanical Engineering, 2021, pp. 223–230
- Gupta, P., Parey, A., To investigate the influence of sound-absorbing materials on the transmission loss of double-wall panel, Materials Today: Proceedings, 2021, 44, pp. 1500–1503
- Kumar, A., Parey, A., Kankar, P.K., Vibration based fault detection of polymer gear, Materials Today: Proceedings, 2021, 44, pp. 2116–2120
- Sharma, V., Parey, A., Singh, A.P., Paul, A., Singh, Y., Detection of Fault in a Bevel Gearbox Under Varying Speed Conditions, Lecture Notes in Mechanical Engineering, 2021, pp. 697–709
- Sharma, V., Parey, A., Effect of Lubricant on the Stiffness and Damping Characteristics in a Single-Stage Gearbox: A Theoretical Analysis, Lecture Notes in Mechanical Engineering, 2020, pp. 185–193
- Sharma, V., Parey, A., Sharma, R.B., Cyclostationary HYPERLINK “https://www.scopus.com/record/display.uri?eid=2-s2.0-85112671435&origin=resultslist&sort=plf-f” Analysis-Based Gearbox Fault Diagnosis Under Varying Speed, Lecture Notes in Mechanical Engineering, 2021, pp. 187–199
- Dewangan HYPERLINK “https://www.scopus.com/authid/detail.uri?authorId=57211494043”, P., Ramteke, D.S., Parey, A., Modeling of Chipped Tooth Fault in Straight Bevel Gears, Lecture Notes in Mechanical Engineering, 2021, pp. 225–235
- Sharma, V., Parey, A., An Approach to Acquire Vibration Signals for Gear Fault Detection, Lecture Notes in Mechanical Engineering, 2021, pp. 153–163
- Gangsar HYPERLINK “https://www.scopus.com/authid/detail.uri?authorId=56414903100”, P., Ali, Z., Chouksey, M., Parey, A., An Intelligent and Robust Fault Diagnostics for an Electromechanical System Using Vibration and Current Signals, Lecture Notes in Mechanical Engineering, 2022, pp. 485–494
Books, book chapters and monographs
- Tandon, N. and Parey, A., Condition Monitoring of Rotary Machines, Chapter
5 in Condition Monitoring and Control for Intelligent Manufacturing, Ed. Wang,
L and Gao, R.X., Springer_Verlag, 2006, pp 109-136.
- Parey, A., and Tandon, N., Fault Detection of Spur Gears Using Vibration
Monitoring, LAP LAMBERT Academic Publishing GmbH & Co. KG, Saarbrucken, Germany, 2010, ISBN 978-3-8383-9034-5
- Parey, A., and Ahuja, A.S., Application of Artificial Intelligence to Gearbox Fault Diagnosis: A Review”,Chapter 24, IGI Global, 2016, DOI 10.4018/978-1-4666-9798-0.ch024
- Sharma, V., and Parey,A., Use of Cyclostationarity Based Condition Indicators for Gear Fault Diagnosis under Fluctuating Speed, Cyclostationarity: Theory and Methods III. Applied Condition Monitoring, vol 6. Springer.
- Saxena,A., Chouksey,M., and Parey,A., Modal analysis of geared rotor system using finite element method, Multi-disciplinary Sustainable Engineering: Current and Future Trends,2016, pp.413-417, Taylor & Francis Group, London.
- Pandya, Y., and Parey A., Theoretical and Experimental Investigation of Spur Gearbox with Cracked Pinion Tooth Using Dynamic Model for Condition Monitoring, Advances in Intelligent Systems and Computing, Volume 1096, 2020, Pages 439-463
- Pandya, Y., and Parey, A., Experimental Study of Sideband Harmonics in Vibration Spectrum of Two-Stage Planetary Gear Box for Condition Monitoring, Advances in Intelligent Systems and Computing, Volume 1096, 2020, Pages 465-471
- Ahuja, A.S., Ramteke, D.S., and Parey, A., Vibration-Based Fault Diagnosis of a Bevel and Spur Gearbox Using Continuous Wavelet Transform and Adaptive Neuro-Fuzzy Inference System, Advances in Intelligent Systems and HYPERLINK “https://www.scopus.com/sourceid/5100152904?origin=recordpage”ComputingVolume 1096, 2020, Pages 473-496
- Ahuja, A.S., Ramteke, D.S., Parey, A., Vibration-Based Fault Diagnosis of a Bevel and Spur Gearbox Using Continuous Wavelet Transform and Adaptive Neuro-Fuzzy Inference System, Advances in Intelligent Systems and Computing, 2020, 1096, pp. 473–496
- Pandya, Y., Parey, A., Theoretical and Experimental Investigation of Spur Gearbox with Cracked Pinion Tooth Using Dynamic Model for Condition Monitoring, Advances in Intelligent Systems and Computing, 2020, 1096, pp. 439–463
- Pandya, Y., Parey, A., Experimental Study of Sideband Harmonics in Vibration Spectrum of Two-Stage Planetary Gear Box for Condition Monitoring, Advances in Intelligent Systems and Computing, 2020, 1096, pp. 465–471
- Dewangan HYPERLINK “https://www.scopus.com/authid/detail.uri?authorId=57211494043”, P., Ramteke, D.S., Parey, A., Model Based Fault Diagnosis in Bevel Gearbox, Applied Condition Monitoring, 2022, 19, pp. 117–133
PhD Guidance
S# |
Name of research scholar |
Title of thesis |
Co-guide |
Year of completion |
1. |
Yogesh Pandya |
Mesh stiffness studies of spur gear pair with tooth root crack |
None |
2013 |
2. |
Vikas Sharma |
Gearbox fault diagnosis under fluctuating speed conditions using vibration analysis |
None |
2017 |
3. |
Ankur Saxena |
Investigation of mesh stiffness and modal characteristics of geared rotor system with defects |
Dr. Manoj Chouksey |
2017 |
4. |
Naresh Raghuwanshi |
Experimental techniques for the measurement of gear mesh stiffness |
None |
2017 |
5. |
Ram Bihari Sharma |
Modelling of acoustic emission generated in spur gear pair and rolling element bearing |
None |
2017 |
6. |
Amandeep Singh Ahuja |
Gear fault diagnosis using artificial intelligence |
None |
2019 |
7. |
Palash Dewangan |
Dynamic modelling of wind turbine planetary gearbox |
None |
2022 |
8. |
Pavan Gupta |
Noise and Vibration control of gearbox |
None |
2022 |
9. |
Vinod Singh Thakur |
Force and Vibration Analysis in Mechanical Preparation of Root Canals Using Endodontic Files |
Dr. Pavan Kankar |
2022 |
10. |
Dada Saheb Ramteke |
Gear fault diagnosis using advanced signal processing techniques |
Dr. Ram Bilas Pachori |
2023 |
11. |
Anupam Kumar |
Fault diagnosis of plastic gears |
Dr. Pavan Kankar |
2023 |
12. |
Pallavi Gautam |
Gear fault diagnosis using acoustic emission technique |
None |
Ongoing |
13. |
Sonu Paroche |
Failure analysis of automotive gearboxes |
None |
Ongoing |
14. |
Santosh Yadav |
Dynamic modelling for gearbox fault detection |
None |
Ongoing |
15. |
Yogesh Andhale |
Gear fault diagnosis using AI and ML techniques |
None |
Ongoing |
M Tech Guidance
S# |
Name of research scholar |
Co-guide |
Year of completion |
1. |
Pravin Rai |
Prof. Neelesh Kumar Jain |
2016 |
2. |
Rajat Kasliwal |
Prof. Neelesh Kumar Jain |
2017 |
3. |
Gaurav Kumar |
Prof. Neelesh Kumar Jain |
2017 |
4. |
Rahul Kashyap |
Prof. Neelesh Kumar Jain |
2017 |
5. |
Vivek Rana |
Prof. Neelesh Kumar Jain |
2018 |
6. |
KUSHAGRA KASTWAR |
None |
2020 |
7 |
SHASHANK CHOUDHARY |
None |
2020 |
8 |
SHIVAM KUMAR |
None |
2020 |
9 |
PANKAJ CHAURASIA |
None |
2022 |
10 |
DESAI UMESH DHANAJI |
None |
2022 |
11 |
Utkarsh Saxena |
None |
2022 |
12 |
IGAVE SAYALI DINESH |
None |
2022 |
13 |
GAIKWAD AKSHAY JAGANNATH |
None |
2022 |
14 |
SHUBHAM KUMAR
|
None |
2023 |
15 |
AMARPRAKASH CHANDRAKANT SINGH |
None |
2024 |
Sponsored Research
S# |
Name of the Project |
Funding Agency |
Amount (Rs) |
Duration |
Role |
1. |
Centre of Excellence in Gear Engineering |
DST FIST |
2,95,00,000 |
2015-2020 |
Member |
2. |
Internal noise measurement, analysis, source identification and design counter measures for trucks and buses. |
DST UAY
|
65,00,000 |
2017-2020 |
PI |
3. |
Design, modeling and diagnostic of wind turbines for sustainable energy efficiency |
DST |
10,80,000 |
2017-2020 |
PI |
4. |
Development of a flexible fault diagnosis technique for induction motor based on artificial intelligence |
TEQIP |
12,90,000 |
2019-2020 |
Co-PI |
5. |
Analysis and control of noise pollution in hospitals |
TEQIP |
21,83,000 |
2019-2020 |
Co-PI |
7. |
Fault detection of gearbox using vibration and acoustic emission analysis |
DST (WOS-A) |
19,40,000 |
2019-2022 |
Mentor |
6. |
Force and vibration analysis in biomechanical preparation of root canals using endodontic file system: In-vitro study |
SERB |
3403400 |
2021-2024 |
Co-PI |
8. |
Noise control of Drones |
SwaYaan Drone/UAS
|
2,50,000 |
2023-2024 |
PI |
Industrial consultancy
S# |
Organization |
Title |
Amount |
Year |
1. |
AIMIL Ltd. Mumbai |
Noise control of HVAC system |
50000 |
2012 |
2. |
Kores (India) Ltd. Pithampur |
Preparation of a report on existing test facilities and testing procedure for drilling rigs |
50000 |
2013 |
3. |
Philips India Ltd |
Vibration measurement and reduction of Philips JMG |
300000 |
2014 |
4. |
Shree Cement, Ajmer |
Root cause analysis of Gear Failure |
300000 |
2014 |
5. |
Simplex Engg & Foundary Works Pvt. Ltd., Bhilai, CG. |
Opinion regarding the rolling mill and auxiliary equipment |
100000 |
2014 |
6. |
AVTEC, Pithampur |
Opinion regarding manufacturing accuracy of gearbox |
100000 |
2015 |
7. |
Liu Gong, Pithampur |
Engine vibration isolation of excavator |
40000 |
2016 |
8. |
Volvo Eicher Commercial Vehicles, Pithampur |
Noise and vibration measurement of gearbox |
40000 |
2017 |
9 |
Sagar Institute of research and Technology |
Analysis of Stress stairs group for tension and compression. |
9,080 |
2018 |
10 |
VE Commercial Vehicle Ltd. |
Vibration mesurement & analysis of truck and Vibration mesurement & analysis of Buses |
42480 |
2019 |
11 |
VE Commercial Vehicle Ltd. |
Vibration mesurement & analysis of hood & Pod |
47200 |
2021 |
12 |
Shri G.S.Institute Of Technology & Science (SGSITS) |
Microhardness Analysis. |
11800 |
2021 |
13 |
Aimil Ltd |
Torsion Analysis |
3540 |
2022 |
Continuing education programs conducted
S# |
Name of the Course/ Conference |
Duration |
1. |
Materials Science and Engineering for Automobile |
Dec 22-23, 2011 |
2. |
Advances in Gear Engineering |
Nov 19-23, 2012 |
3. |
Bearing and Gear Fault Diagnosis |
Mar 21- 2014 |
4. |
Condition Monitoring of Rotating Machine Elements |
Dec. 21-23, 2015 |
5. |
Condition Monitoring of Mechanical Systems using Advance Signal Processing |
Jun 27-28, 2016 |
6. |
Condition Monitoring of Mechanical and Electrical Systems using Advanced Signal Processing Techniques |
06-07 March 2017 |
7. |
Advanced Signal Processing Techniques for Fault Detection of Mechanical and Electrical Systems |
10-11 March 2018 |
8. |
Bearing and Gear Fault Diagnosis |
26-27 March 2018 |
9. |
Artificial Intelligence and Advanced Signal Processing Techniques for Engineering Applications |
05-07 October 2018 |
10. |
Research and Development in Condition Monitoring of Rotating Machines |
10-12 December 2018 |
11. |
Vibration Monitoring Techniques for Machinery Fault Diagnosis |
18-19 March 2019 |
12. |
Vibration Monitoring of Mechanical Systems |
29-31 Oct’ 2020 |
13. |
Industrial Noise & Vibration Control |
26-28, Nov 2020 |
14. |
Condition Monitoring of Rotating Machines using Advanced Signal Processing Techiques |
21-23, Dec 2020 |
15. |
Advance in Condition Bases Maintenance using Vibration and Noise Monitoring |
19-21, Feb 2021 |
——————————————————————————————————————————————————————————————————————————-
February 17th, 2022 | by admin_me_wp | posted in
Uncategorized
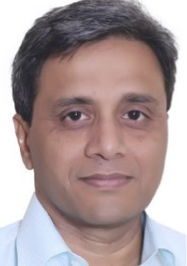
Faculty Name: Dr. Suhas S. Joshi
Designation: Professor, Director
Email: ssjoshi@iiti.ac.in Office Contact: +91 731-6603130
Research Areas:
- Modeling machining of ‘difficult-to-machine’ materials (MMCs, Inconel, Titanium)
- Modeling and development of micro-machining processes.
- Laser micro-machining, LIGA and Nano-polishing.
Biosketch:
Dr. Suhas Joshi is currently the Director, IIT Indore. He is a Fellow of the Indian National Academy of Engineering, and the National Academy of Sciences.
Prior to joining IIT Indore as the Director, Dr. Joshi served as a Rahul Bajaj Chair Professor in the Department of Mechanical Engineering at IIT Bombay. He also served as the Dean of Alumni and Corporate Relations (2017-2022) and the Head of Mechanical Engineering Department (2014-1207) at IIT Bombay. He served as a Visiting Faculty in Mechanical Science and Engineering at the University of Illinois at Urbana-Champaign, USA (2005-06).
Dr. Joshi has been a recipient of BOYSCAST fellowship of Govt. of India (2002), ‘Best Faculty’ award of Mech. Eng. Dept., IIT Bombay (2007), and ‘Dr. P. K. Patwardhan Technology Development Award’ of IIT Bombay (2008).
Dr. Joshi works on improving the productivity and quality of multi-scale machining processes through physics-based modeling and characterization. He has undertaken over 38 research, consultancy, and infrastructure development projects sponsored by aerospace, nuclear, defense, and private organizations in India. He has established excellent research infrastructure for micromachining, laser micro-machining, and titanium machining. During 2009-14, he spearheaded the establishment of ‘National Centre for Aerospace Innovation and Research (NCAIR)’, at IIT Bombay as its founding Principal Investigator. The centre is an industrial consortia mainly sponsored by Govt. of India, The Boeing Company, and IIT Bombay.
Dr. Joshi has served as an Associate Editor of Trans. ASME, Journal of Manuf. Sci. and Eng. (2007-14). He is presently an Associate Technical Editor of Machining Sci. and Technol. (Taylor and Francis) (2010-) and, the Editorial Board Member of International Journal of Machine Tools and Manuf. (Elsevier) (2013-2018) and Indian Journal of Engineering & Materials Sciences, CSIR-NISCAIR (India) (2015-).
Dr. Joshi has supervised a post-doctoral and 18 doctoral students. He is presently guiding another 6 doctoral students for their Ph.D. He also has supervised more than 112 masters dissertations at IIT Bombay. Dr. Joshi has over 300 publications including 179 in referred international journals and five book chapters to his credit. He has a phenomenal h-index of 41 (Google Scholar).
February 17th, 2022 | by admin_me_wp | posted in
Uncategorized
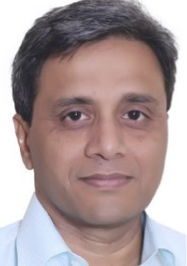
Faculty Name: Dr. Suhas S. Joshi
Designation: Professor, Director
Email: ssjoshi@iiti.ac.in Office Contact: +91 731-6603130
Research Areas:
- Modeling machining of ‘difficult-to-machine’ materials (MMCs, Inconel, Titanium)
- Modeling and development of micro-machining processes.
- Laser micro-machining, LIGA and Nano-polishing.
Biosketch:
Dr. Suhas Joshi is currently the Director, IIT Indore. He is a Fellow of the Indian National Academy of Engineering, and the National Academy of Sciences.
Prior to joining IIT Indore as the Director, Dr. Joshi served as a Rahul Bajaj Chair Professor in the Department of Mechanical Engineering at IIT Bombay. He also served as the Dean of Alumni and Corporate Relations (2017-2022) and the Head of Mechanical Engineering Department (2014-1207) at IIT Bombay. He served as a Visiting Faculty in Mechanical Science and Engineering at the University of Illinois at Urbana-Champaign, USA (2005-06).
Dr. Joshi has been a recipient of BOYSCAST fellowship of Govt. of India (2002), ‘Best Faculty’ award of Mech. Eng. Dept., IIT Bombay (2007), and ‘Dr. P. K. Patwardhan Technology Development Award’ of IIT Bombay (2008).
Dr. Joshi works on improving the productivity and quality of multi-scale machining processes through physics-based modeling and characterization. He has undertaken over 38 research, consultancy, and infrastructure development projects sponsored by aerospace, nuclear, defense, and private organizations in India. He has established excellent research infrastructure for micromachining, laser micro-machining, and titanium machining. During 2009-14, he spearheaded the establishment of ‘National Centre for Aerospace Innovation and Research (NCAIR)’, at IIT Bombay as its founding Principal Investigator. The centre is an industrial consortia mainly sponsored by Govt. of India, The Boeing Company, and IIT Bombay.
Dr. Joshi has served as an Associate Editor of Trans. ASME, Journal of Manuf. Sci. and Eng. (2007-14). He is presently an Associate Technical Editor of Machining Sci. and Technol. (Taylor and Francis) (2010-) and, the Editorial Board Member of International Journal of Machine Tools and Manuf. (Elsevier) (2013-2018) and Indian Journal of Engineering & Materials Sciences, CSIR-NISCAIR (India) (2015-).
Dr. Joshi has supervised a post-doctoral and 18 doctoral students. He is presently guiding another 6 doctoral students for their Ph.D. He also has supervised more than 112 masters dissertations at IIT Bombay. Dr. Joshi has over 300 publications including 179 in referred international journals and five book chapters to his credit. He has a phenomenal h-index of 41 (Google Scholar).
January 18th, 2021 | by admin_me_wp | posted in
Uncategorized
October 23rd, 2019 | by admin_me_wp | posted in
Uncategorized
- Ms. Shalini Singh working with Dr. I.A. Palani, Associate Professor from the Discipline of Mechanical Engineering has received ISSS postgraduate student award for the year 2019 from Institute of Smart Structures and Systems(ISSS), Department of Aerospace Engineering, IISC Bengaluru.
- International Conference on Precision, Meso, Micro & Nano Engineering COPEN-11 (December 12-14, 2019)
- Samsung Innovation award : Winner – Book 360 (Cash prize 1.5 Lakhs) By – Ram Mohril, Mentored by Dr. Bhupesh Kumar Lad and 1st Runner up – Tree Climbing Quadruped (Cash prize 1.2 lakhs) By – Chaitanya Mehta, Mentored by Dr. Devendra Deshmukh.
September 17th, 2019 | by admin_me_wp | posted in
Uncategorized
http://copen2019.iiti.ac.in/
March 27th, 2019 | by admin_me_wp | posted in
Uncategorized
http://copen2019.iiti.ac.in
May 31st, 2018 | by admin_me_wp | posted in
Uncategorized
April 11th, 2018 | by admin_me_wp | posted in
Uncategorized